Apollo's Vap-X 3 Phase and Vap-X Gas Blend Can Help Bring Shut-In Production Back Online
Challenge
Find a solution for hydrogen sulfide (H2S) treatment for H2S oil/gas in the Permian Basin for shut-in legacy wells.
Solution
Apply Apollo's Vap-X™ suite of chemistries to improve, manage, and mitigate H2S and CO2 in oil/gas/water phases or each individually. It will allow producer to manage gas in the midstream sales line.
Results
- Reduce H2S and CO2 levels to allow for gas sales.
- Improve overall safety and integrity of company assets.
- Demonstrated the effectiveness of Apollo's Vap-X™ suite of chemistry at mitigating H2S and CO2 with minimal side effects.
Apollo's Vap-X™ 3 phase and Vap-X™ gas blend can help bring shut-in production back online.
Multiple Treatment Options Utilizing Both Chemistries
Reduce Hydrogen Sulfide in sour crude oil and gas.
Hydrogen Sulfide is naturally produced from the Permian Basin Formation. The levels can range from a few ppm up to 250,000 ppm hydrogen sulfide and must be reduced to below pipeline specifications. In addition to reducing product value, hydrogen sulfide exposes producers to environmental and safety risk. It also can increase the chance of corrosion.
Producer in West Texas currently deals with high levels of H2S. In some particular batteries levels are so high that it has forced producers to leave wells shut-in. Apollo suggested treating the Hydrogen Sulfide using their Vap-X 3 Phase product which will reduce the H2S in gas phase (as well as oil and water phase)thus allowing for a lower gas spec. This reduced level can then be sold to midstream for gas processing. Apollo, then utilizes its √ap-X™ Oil Blend product to treat the oil stream after separation to < 10 ppm of H2S,therefore meeting for pipeline specifications and midstream sales requirements.
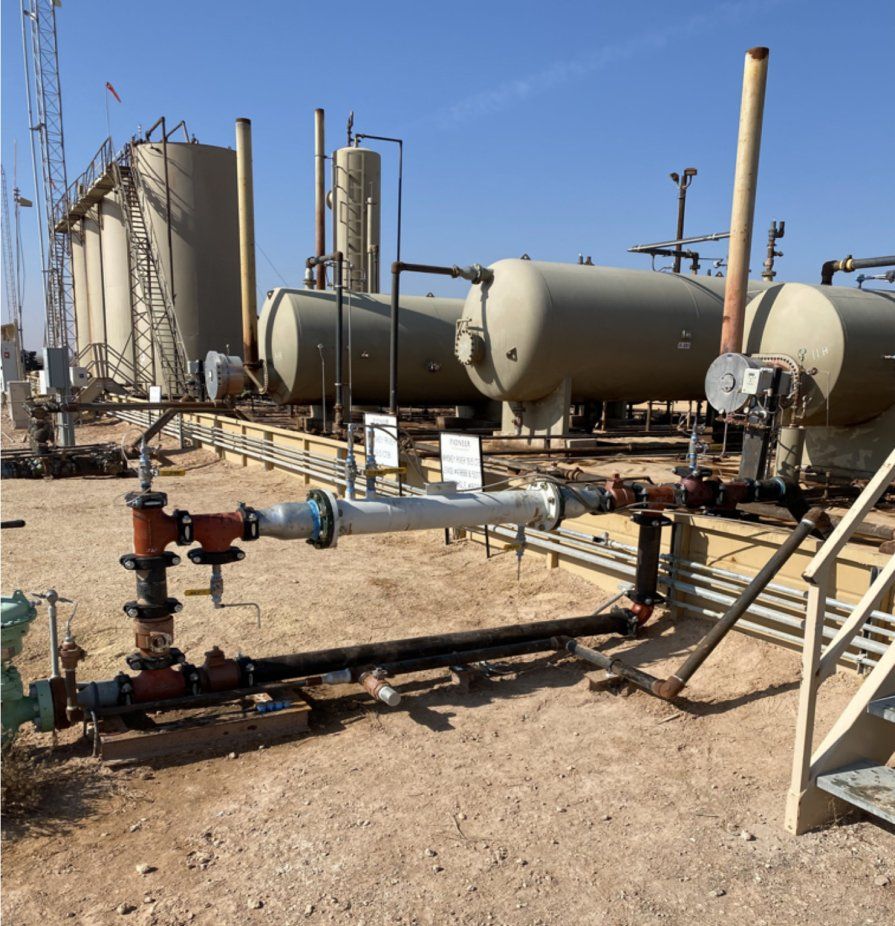
3 Foot Static Mixer Installed
The initial pilot began on January 29, 2022. The goal of the pilot was to return to the well back to continuous production with the oil level of H2S below 10ppm and the gas level of H2S with 50% reduction. The picture above shows the well coming into the facility as a commingled stream. Apollo suggested a 3 foot static mixer to help with blending the chemistry into all three phases which in turn would lower the dosage rate was installed that allowed Apollo to introduce Vap-X 3 phase blend into the stream. Apollo also asked for the installation of three different testing ports. These ports allow Apollo to monitor the streams for H2S ppm reduction, water ph, along with fluid rates. Apollo's Vap-X 3 phase reduces H2S and CO2 in all three streams. The initial startup of the well came with numerous challenges since the well has been shut-in for an extended period of time. We experienced very sporadic flows as well as very high H2S and CO2 raw numbers upon startup. The initial numbers were 250,000 ppm of H2S as well as 250,000 ppm of CO2.
The Vap-X 3 phase chemistry is designed to greatly reduce both H2S and CO2 in all three streams. This particular well is very unique in two different ways. First, the oil/water phase H2S and CO2 is typically lower than gas phase. This was not the case for the well. This required higher dosing. Second, the CO2 concentration in the oil and gas was much higher than anticipated requiring a higher dosage rate (Vap-X is not selective for H2S only but will also mitigate CO2). We brought the well online on 01/29/2022. Production rates and H2S concentrations fluctuated a lot during the first two weeks of testing. Production shut-ins occurred a couple of times during the test. Initial dosage rates of Vap-X 3-Phase were in the 70-75 gallons per hour. Reductions in H2S and CO2 occurred almost immediately and ranged between 40%-69% over the first 7 days. The tables below show results sampling during the test. The raw and the treated H2S numbers represent the concentrations in the gas phase. Apollo also measured the water pH in the mixer and at the free water knockout to monitor for conditions that would allow for potential solids to form.
Date | Time | Raw H2S PPM | Treated H2S PPM | Mixer PH | Knock PH |
---|---|---|---|---|---|
01/29/22 | 6:34 PM | 150,000 | 78,000 | NA | NA |
01/30/22 | 12:47 PM | 150,00 | 78,000 | 9.5 | 8.5 |
01/30/22 | 1:21 PM | SHUT-IN |
As the well came back online on 1/31/2022 we once again noticed high fluctuations in the raw ppm of H2S. However, one of the unique characteristics of the Vap-X™ suite of chemistries is that they are able to deal with burps(high fluctuations) of H2S unlike anything on the market. Which makes it ideal for wellhead application especially when dealing with elevated H2S levels that tend to hit pockets of high H2S occasionally (ie..100k ppm jumping to150k ppm)
Date | Time | Raw H2S PPM | Treated H2S PPM | Mixer PH | Knock PH |
---|---|---|---|---|---|
01/31/22 | 6:04 PM | 110,000 | 52,000 | 9 | 6.2 |
02/01/22 | 9:05 AM | 170,000 | 65,000 | 9 | 6.79 |
02/01/22 | 2:10 PM | 130,000 | 40,000 | 8.77 | 6.78 |
02/01/22 | 8:03 PM | 120,000 | 60,000 | NA | 7 |
02/02/22 | 9:53 AM | 110,000 | 55,000 | NA | 7.89 |
02/02/22 | 12:29 PM | SHUT-IN |
We received word from midstream company that we had to shut-in due to constraints at their plant due to another customer. Then due to weather (cold front) we had to keep the well shut-in because the pumps had to be defrosted. Once that got situated we went back to pumping chemistry on 2/3/2022 at 2:30 pm. We continued to get very good results however Apollo felt dosage could be improved from the 70-75 gallons/hour.
Date | Time | Raw H2S PPM | Treated H2S PPM | Mixer PH | Knock PH |
---|---|---|---|---|---|
02/03/22 | 4:24 PM | 118,000 | 55,000 | NA | 7.25 |
02/03/22 | 6:11 PM | 120,000 | 53,000 | NA | 7.7 |
02/04/22 | 2:42 PM | 115,000 | 55,000 | NA | 7.5 |
Apollo working along with the producer suggested utilizing an additional chemistry from the Vap-X™ suite. The Vap-X™ gas blend chemistry which would be introduced via the inlet to the scrubber. Apollo would also introduce a water wash into line to insure flow and allow any contaminants (salt mainly) the ability to be absorbed back into the water phase. This is an application that Apollo has applied for a patent, due to the application and chemistry. Apollo utilized both Vap-X™ 3 phase and Vap-X™ gas only. Apollo continued to inject Vap-X™3 phase chemistry via the static mixer point. While simultaneously polishing the gas via the injection points before the scrubber as seen below.
The amount of water needed for the water wash is a formula based on the expected MMCF, as well as the H2S and CO2 ppm associated with the gas stream. Since this stream has an estimated flow of around 1.2 MMCF per day as well as 15% of both H2S and CO2 respectively, the water utilized via this application requires a large dosage pump similar to the chemistry. The picture below shows the pump configuration at the scrubber injection for the gas only stream as well as the chemical pump for the three phase injection.
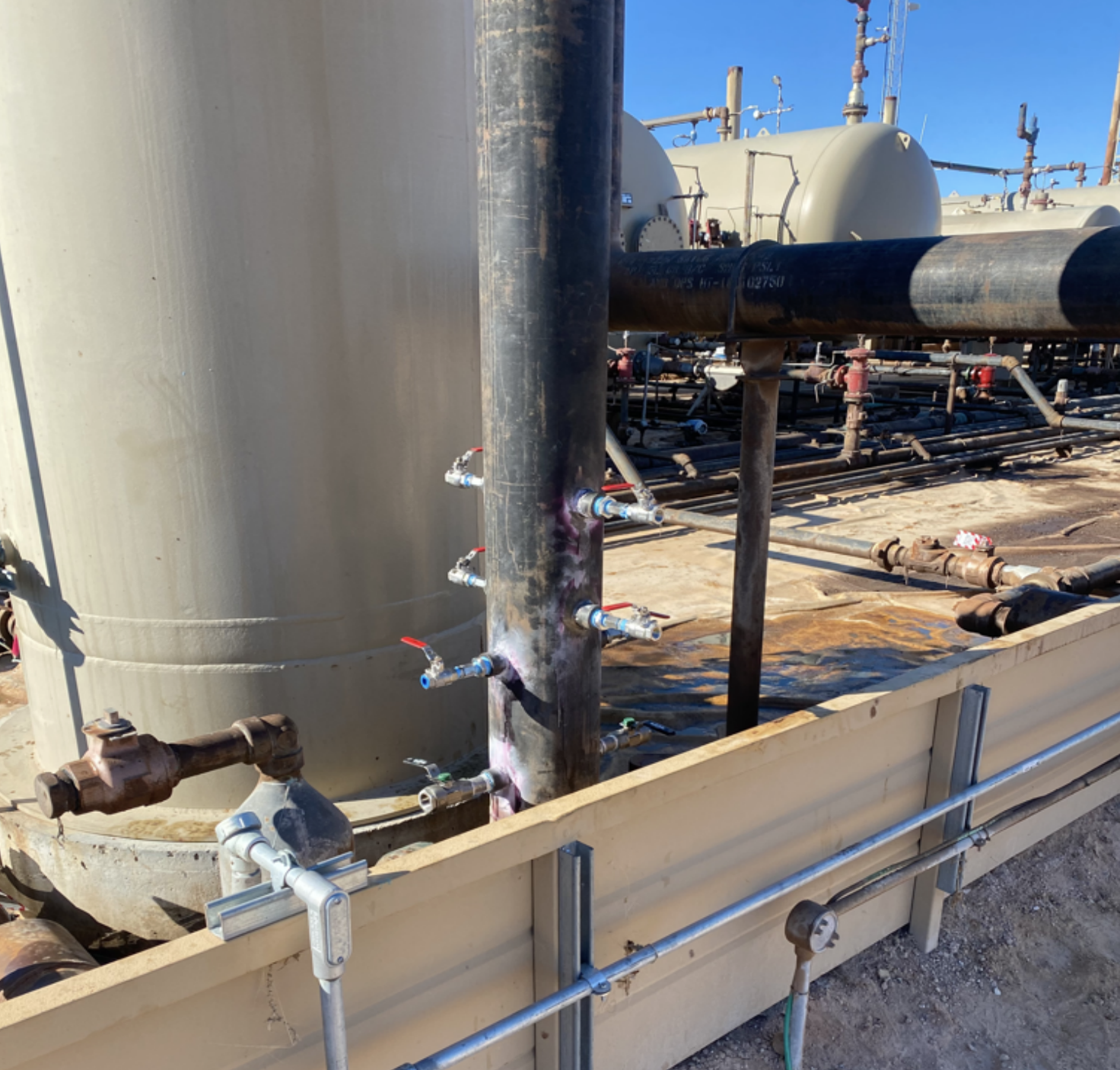
Patent Pending Water Wash Application
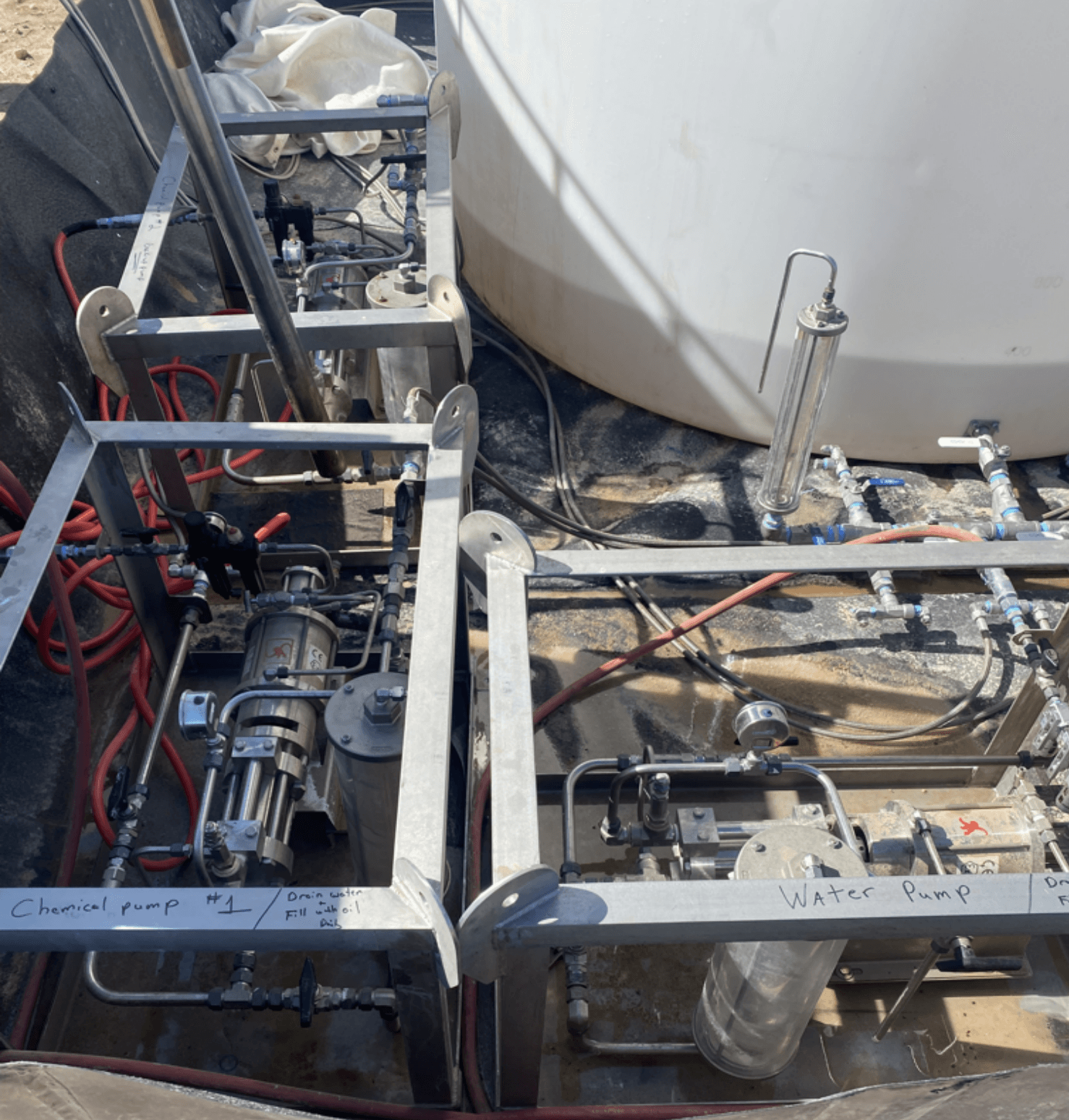
Dosage Pumps for Vap-X™ 3 Phase, Vap-X™ Gas Blend, Water Wash
As we started up the initial injection point at the inlet of the scrubber the well continued to spike up and down. During the night of Feb 5th and morning of Feb 6th the raw ppm of H2S spiked to over 200,000 ppm. However with the injection of the Vap-X™ suite of chemistries (VapX™ 3 phase and Vap-X™ gas blend) at the two different spots we noticed it was able to handle the spikes easier. We were; however, continuing to use 70 gal/hour between the two injection points.
Date | Time | Raw H2S PPM | Treated H2S PPM | Mixer PH | Knock PH |
---|---|---|---|---|---|
02/05/22 | 12:34 PM | 162,000 | 80,000 | NA | 7 |
02/06/22 | 10:41 AM | 108,000 | 57,000 | NA | 7.67 |
02/06/22 | 4:31 PM | 107,000 | 55,000 | NA | 7.68 |
02/07/22 | 7:22 AM | 110,000 | 57,000 | NA | 7.09 |
From 2/8 to 2/10 the well was shut-in. After discussions of inconsistencies between producer and Apollo, producer started to realize the inconsistencies of the well flow was due to the ESP (Electrical submersible pump) having outdated software. The decision was made that we needed to get some consistent raw H2S numbers before we started to introduce chemical back into the system. Apollo also after analyzing our data from the previous two weeks wanted to introduce the Vap-X gas blend only thru the injection points at the inlet of the scrubber (no longer use Vap-X™ 3 phase). The morning of 2/11 is when the well would come back online and the raw H2S data would be collected.
Date | Time | Raw H2S PPM | Treated H2S PPM | Mixer PH | Knock PH |
---|---|---|---|---|---|
02/11/22 | 7:00 AM | 121,000 | NA | NA | NA |
02/11/22 | 8:00 AM | 121,000 | NA | NA | NA |
02/11/22 | 9:00 AM | 121,000 | NA | NA | NA |
02/11/22 | 10:00 AM | 119,000 | NA | NA | NA |
02/11/22 | 11:00 AM | 116,000 | NA | NA | NA |
As the well stabilized and it seemed to be running around 120,000 ppm of H2S consistently Apollo was allowed to reintroduce the chemistry as Vap-X™ gas blend only via the injections on the inlet of the scrubber. Apollo instantly noticed a reduction of chemistry from the 70 gal/hour down to 55 gal/hour at initial startup. This was over a 20% reduction compared to the other two previous applications. However on 2/12 Apollo was able to reduce the chemistry usage another 10 gallons/hour down to 45 gal/hour. By switching to a gas only application for the well Apollo was able to reduce the chemistry over 40% from the initial 75 gal/hour down to 45 gal/hour. Apollo was able to maintain this dosage for all of 2/12 and into the morning of 2/13. However the well continued to deal with sporadic flow due to the software being outdated. It was decided to shut-in the well to change a back pressure valve.
Date | Time | Raw H2S PPM | Treated H2S PPM | Mixer PH | Knock PH |
---|---|---|---|---|---|
02/11/22 | 1:32 PM | 120,000 | 70,000 | NA | NA |
02/11/22 | 3:07 PM | 120,000 | 62,000 | NA | NA |
02/12/22 | 10:07 AM | 128,000 | 64,000 | NA | NA |
02/12/22 | 3:11 PM | 120,000 | 52,000 | NA | NA |
02/13/22 | 8:09 AM | SHUT-IN |
As Apollo was monitoring the well it also noticed the gas stream CO2(which fluctuated between 80,000 to 120,000ppm) was consistently around 2% after treatment. Producer informed Apollo that the midstream company views H2S and CO2 as the same meaning they take the combined ppm for their threshold limits. This is a HUGE benefit to the Vap-X™ suite of chemistries because we are getting the H2S reduction that has been well documented as well as a significant reduction in CO2 as well. As Apollo continued to run the chemistry on 2/16 they noticed the reduction was basically the same utilizing 45 gal/hour or 40 gal/hour. After much trial in the field Apollo has came to the conclusion for this particular well the best application is utilizing the inlet injection at the scrubber. Apollo during the field trial also was able to reduce the dosage from 75 gal/hour down to 40 gal/hour saving the producer substantial money.
Date | Time | Raw H2S PPM | Treated H2S PPM | Mixer PH | Knock PH |
---|---|---|---|---|---|
02/16/22 | 9:53 AM | 121,000 | 55,000 | NA | NA |
02/16/22 | 1:56 PM | 118,000 | 55,000 | NA | NA |
02/16/22 | 5:01 PM | SHUT-IN |
After the successful test Apollo met with the producer on 2/17. During that meeting it was decided to setup the Whiskey River 19.5 battery for permanent injection. Apollo asked producer to add static mixers into the other two headers coming into the battery. They also suggested to the producer that some type of automation would be needed so that if the well shut-off the chemical would do the same. Producer agreed to put a valve to cut off air supply to the dosage pumps. Apollo also stated that depending on the treatment of the other wells (meaning how much Vap-X™ 3 phase could be utilized before the scrubber) would determine if an additional scrubber would need to be added to deal with the liquid of the chemical as well as the water from the water wash. Apollo is hoping that the other 4 wells that come into the battery will utilize some of the Vap-X™ 3 phase chemistry which would lower the Vap-X™ gas only chemistry used. However, due to the Vap-X™ suite of chemistry the producer has many options for optimal reduction with minimal chemistry.
As Apollo continued to treat the well on 2/18-2/19 utilizing the injection points at the inlet of the gas scrubber the reduction in H2S and CO2 was continuing to stabilize. Apollo was able to continue to get the reduction at the new dosage rate of 40 gal/hour. In the early morning hours of 2/20 the well shut-in. Since we did not have any automation setup to turn the pumps off, the chemical as well as the water wash continued to run even though there was no gas present. Due to this there was a buildup of solids (salt) at the scrubber dump. Samples were taken and dissolved back in water to verify that salt was the issue. When the proper shut off valves are installed for the chemical pumps this issue will not happen.
Date | Time | Raw H2S PPM | Treated H2S PPM | Mixer PH | Knock PH |
---|---|---|---|---|---|
02/17/22 | 11:49 AM | 112,000 | 50,000 | NA | NA |
02/18/22 | 3:58 PM | 122,000 | 55,000 | NA | NA |
02/19/22 | 10:07 AM | 118,000 | 60,000 | NA | NA |
02/19/22 | 2:53 PM | 120,000 | 62,000 | NA | NA |
The testing for the well was very successful. If we look at an average of 150,000 ppm of both H2S and CO2 and the ability to get these elements down to 50,000 ppm at the sale lines is a monumental leap in chemistry ability. If we are able to quantify these results with 40 gal/hour, then we would be able to deal with H2S < $1.75 Lbs/S and CO2 < $1.75 Lbs/C. Apollo feels as other wells come online in this battery we will see a continued drop in price for Lbs for both elements. By utilizing the Vap-X suite of chemistry Apollo feels we will be able to help the producer tap into roughly 15,000 bbl/day of shut-in production with minimal Cap-X outlay. This particular well proved 800 of such barrels.
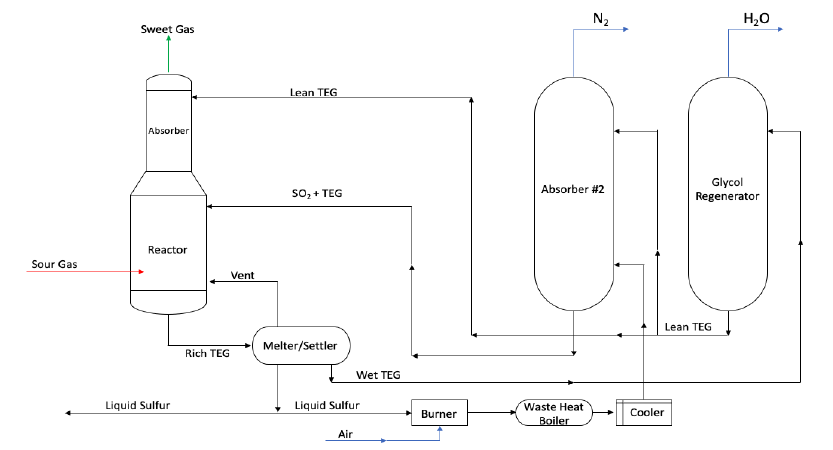
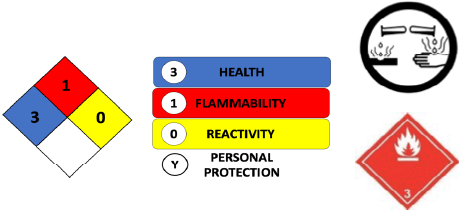
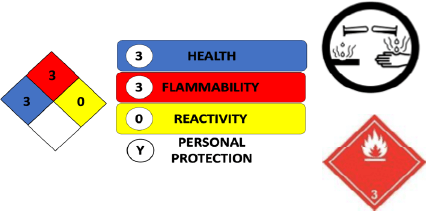
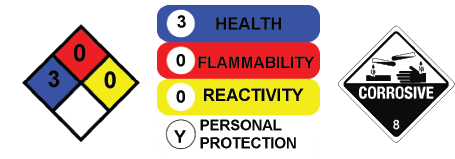